materials for special requirements
Special requirements such as corrosive or high temperature environments often require the use of materials designed for these applications. These materials, in general, have lower tensile strength than standard materials and should only be, if absolutely necessary. These springs have a lower overall height than comparable sizes made of standard materials resulting in lower spring force. This must be taken into consideration using these materials.
Corrosion Resistant Steels
X 10 CrNi 18-8 (1.4310): This chrome nickel alloyed steel as per DIN EN 10151 is the material most used for corrosion resistant springs. Because of its austenitic structure with ferritic inclusions, it cannot be hardened in the usual way, but by cold forming it can obtain the strength required for disc springs. Considerable cold forming in necessary and the strength reduces with increasing thickness. Therefore, the material is normally not available thicker than 2.5mm. In fact, springs can only be supplied to this thickness. Whereas the material in the soft condition is hardly magnetic, the cold working process will make it more or less magnetic again, making it unsuitable for completely non-magnetic springs.
X 7 CrNiAI 17 7 (1.4568): This steel as per DIN EN 10151 precipitation hardened produces an austenitic/ferritic structure. It will also be processed in the work hardened condition and may be hardened by subsequent heat treatment. A disadvantage compared to steel 1.4310 is the lower corrosion resistance and sensitivity to stress corrosion. We therefore only recommend its use for springs over 2.5mm thickness if no other material is available.
X 5 CrNiMo 17 12 1 (1.4401): The strength of this material is somewhat less than either of the two forgoing. Not withstanding that it offers higher corrosion resistance and lowest magnetism. Although also contained in DIN 17224, it is often difficult to obtain and therefore only seldom used.
Steels for Higher Temperatures
When considering springs for use at higher working temperatures it must be remembered that both tensile strength and Young’s modulus ‘E’ are reduced compared with the values at room temperature.
X 22 CrMoV 12 1 (1.4923): This heat treatable chrome-molybdenum steel has been used very successfully for heat resistant disc springs. Springs of 1.5 to 6mm thickness are made from strip or plate. For thicker springs, forged rings can be used.
Figure 38 shows the mechanical properties and Young’s modulus ‘E’ with respect to temperature. It should be noted that with a chrome content of 12% this steel is not corrosion resistant.
Figure 38 - click to enlarge 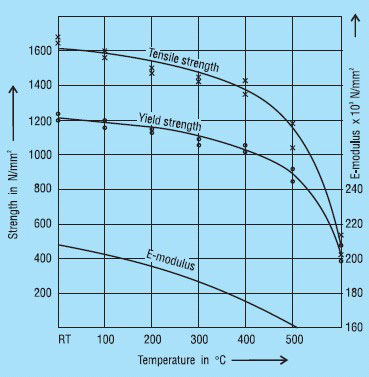
X 39 CrMo 17 1 (1.4122): Here we have a chrome-molybdenum alloyed heat treatable martensitic steel which is also suitable for corrosion resistant springs. Because of the molybdenum is may be used up to 400oC. However, at these temperatures both the tensile strength and ‘E’ are reduced.
In order to achieve the required properties, this steel must be hardened to higher values which raises the question of stress corrosion. Unfortunately, in the light of current technical knowledge we cannot completely discount the possibility of delayed brittle fracture.
Copper Alloys
Copper alloys are absolutely non-magnetic and have very good electric conductivity. Moreover, they are corrosion-resistant against many media. These characteristics make them suitable for many disc spring applications.
CuSn 8 (2.1030): Tin bronze as per DIN EN 1654 is an alloy of copper and tin, which obtains is spring properties from cold working. The tensile strength is certainly lower than spring steel and the ‘E’ modulus is only 55% of the value for steel. This must be considered in the spring calculation and allows their use in applications where very low spring loads are required.
CuBe 2 (2.1247): Beryllium copper is an outstanding spring material. This heat treatable alloy has strength values comparable with steel. However, Young’s modulus ‘E’ is only 60% of that for steel. It has very good corrosion resistance and may be used at very low temperatures nearing absolute zero.
Nickel and Cobalt Alloys
From the large number of nickel-chrome and nickel-chrome-cobalt based alloys some have achieved importance for disc springs. By alloying the aluminium, titanium and/or niobium/tantalum they are precipitation hardenable. These materials are very tough, that is to say they have high strength and a low elastic ration. Therefore, the probability of more set in the spring must be considered. Against this are the outstanding fatigue properties. With correct spring proportions this is good over the total spring travel. Because of the material composition they have outstanding corrosion resistant to many media. All these alloys are very expensive and often hard to work, and as a rule have long deliveries. They are therefore only used where no other material is suitable due to technical considerations.
NiCr 20 Co 18 Ti (Nimonic 90) (2.4632, 2.4969): These nickel-chrome-cobalt alloy gives the least problems in processing and is therefore the most often used. It has very good heat resistance and can be used up to 700oC with suitable dimensioning.
NiCr 15 Fe 7 TiAi (Inconel X 750) (2.4669) and NiCr 19 NbMo (Inconel 718) (2.4668): These nickel-chrome alloys are practically cobalt-free, and are therefore used in reactor applications. The hardening process is difficult and expensive. The application is limited and only used in special cases. NIMONIC and INCONEL are trade names of Inco Alloys International.
DURATHERM 600: This is a heat treatable alloy of the cobalt-nickel series with outstanding mechanical properties. At a temperature of 0oC the material in non-magnetic. It can be used at very high temperatures (600oC and over). The very high price of this alloy limits its use to very special applications. DURATHERM is a trade name of Vacuumschmelze GmbH in Hanau.
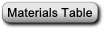