design & characteristics of radial ball bearings
In the majority of applications the size of the ball bearing is selected according to space considerations. Usually the load capacity which the selected bearing provides is more than adequate for the continuous loads to which it is subjected. In extreme cases, or which severe vibration or shock loading is known to occur, the load carrying capability should be checked.
The form which the bearing takes is entirely determined by the overall design philosophy.
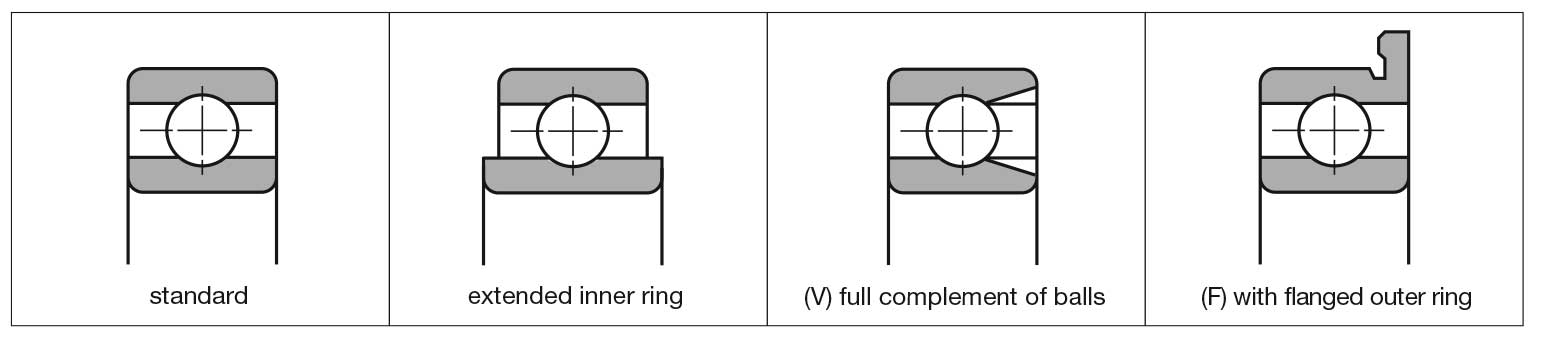
Open or closed – is the bearing likely to become contaminated? Is escape or outgassing of lubricant an issue?
Normal or extended inner – is there sufficient clearance axially between rotating and stationery components?
Load – single low radial ball bearings with balls separated by a cage can support radial loads, axial loads and tilting moments. A full complement V-type ball bearing can support only radial loads and some low axial loads.Generally a full complement bearing is used when a higher radial load is required than the standard bearing provides.
Speed – maximum permissible speeds for ball bearings are mainly related to the bearing design and size, cage type, bearing internal clearance, method and type of lubrication, manufacturing accuracy, sealing methods and loads.
Torque and noise level – single low radial ball bearings are precision components and have low torque and noise levels.
Inclination or inner/outer rings – shaft and housing seats with poor accuracy, fitting errors and shaft bending might cause inclination between the inner and outer rings although the internal clearance of the bearing will permit this to a certain extent. Generally, the maximum permissible inclination between the inner and outer rings is approximately 1 in 300.
Toughness – bearings under load deform elastically at the contact point between the rolling element and bearing ring. This is influenced by the bearing type, size, form and load.
Installation and removal – the single row radial ball bearing is a non-separable bearing. Therefore, shafts and housings should be so designed to enable bearing inspection and replacement when necessary.
Axial location – improved axial location is obtained with Thrust type bearings.
Two important internal parameters which must be considered and specified when a bearing is selected are:
Radial play & internal clearance – the total diametrical movement from contact at one side between rings and balls to similar contact at the other side. It is normally stated in increments of tenths of a thousandth of an inch or microns. This parameter effects the torque level, the axial movement, the load carrying capacity, especially in an axial direction and, according to installation, the noise level and smoothness of the bearing.
Lubrication – the choice of oil or grease and the particular type of each, has an influence on the bearing performance. Noise level, speed, environment temperature, load and life are some of the various factors which should be considered when selecting lubricant.